Tuesday, August 31, 2010
What can driving on the Moon teach you about peripheral integration?
Quanser's Hexapod was on display along with QUARC and the Active Suspension System. We displayed how the Hexapod could be used as a six degree of freedom motion platform, simulated vehicle motion.
Personally, the Hexapod is my favorite - it has a large payload capacity (250 kg), can be used as a shake table or parallel robot, can connect to a regular power supply, and uses a simple USB cable for data transfer. In our setup, we had it tied through QUARC to a visualization of a lunar surface. Attendees could sit on the Hexapod, grab a joystick, and go for a joy ride. As the controller was running, we had the ability to toggle on and off the active suspension of the lunar buggy and occupants were able to feel the moon bumps much more.
The Active Suspension Experiment was also on display - along with a virtual version of the experiment. It showed how students could design controllers to dampen out vehicle vibration.
The glue to these different systems was QUARC. QUARC can bring together complex systems and pair them with peripherals like joysticks, motion tracking cameras, and haptic devices. It can also allow someone to create a virtual environment to interact with their controller.
After the conference, ten lucky attendees had a chance to experience the magic behind the scenes and tour Quanser's headquarters, taking advantage of our open invitation earlier this summer.
Video shot by another one of our talented engineers, Pasha Javid
Tuesday, August 17, 2010
Unmanned Vehicle Systems Lab - AIAA GNC 2010
What are some potential applications of unmanned vehicle systems?
Some of my favorite applications include Search & Rescue, Space and Agricultural Monitoring. Unmanned vehicle systems may also be used for telecommunications, traffic monitoring, security, surveillance and defense. As I eluded to in a previous presentation at the ECEDHA conference, computers are becoming smaller and faster at an exponential rate. This trend, coupled with the explosion of innovation in the field of Mechatronics, will lead to a world consisting of unmanned vehicle systems, everywhere. Most of you are already aware of the DARPA Grand Challenge. Just imagine, in a few short years, you will be able to hop into your personal helicopter, tell it that you wish to visit (fill in the blank), and voila, it takes you there effortlessly! Think it’s too farfetched? Here’s something that Amin, a colleague of mine, recently told me about: NASA’s Puffin. Check it out!
Quanser’s UVS Lab is a multi-purpose research and development workshop for autonomous unmanned aerial and ground vehicles. This turn-key solution comes equipped with QUARC (real-time control and multi agent mission development frameworks), Ground control station, Qball-X4, Embedded computer systems and inertial measurement units, Qbot unmanned ground vehicles and Localization system with cameras. Research applications include motion planning, sensor fusion, multi-agent navigation and formation control. The first component is the ground station computer which includes QUARC, Quanser’s real time control software. QUARC gives you the ability to use Matlab/Simulink and Real Time Workshop to develop all of your controller algorithms and then download and execute them remotely on your target vehicle. All of the control design, mission planning and inter-vehicle communication is seamlessly wirelessly downloaded onto the vehicle; there’s no need to write low level code. The Qball-X4 is Quanser’s indoor unmanned air vehicle and is outfitted with a Quanser made data acquisition card, called the Hi-Q. The Hi-Q is specifically designed to fly an unmanned air vehicle and is equipped with a range of sensors: gyroscopes, accelerometers, GPS, sonar and pressure sensors. To read more or to request a quote, click here.
Advantages of Indoor vs Outdoor?
Our founder, Dr. Jacob Apkarian, before he started Quanser more than 20 years ago, contributed significantly to the development of several key space projects, including control systems for the Canada Space Arm and components of the Space Station. To learn more about Quanser’s past experience with outdoor systems and the evolution of Quanser’s UVS platform, click here to read an interview with Jacob and Cameron, our lead UVS R&D Engineer. More recently, over the past 6 years, Jacob and Cameron have led our innovate R&D team on a relentless pursuit to engineer an open-architecture unmanned vehicle systems lab designed specifically for academic advancement. At the AIAA conference, I presented this Unmanned Vehicle Systems Lab alongside Amin, Cameron and Ali, three of our UVS specialists. Our team has extensive experience working with both outdoor and indoor labs. One of the major challenges with outdoor systems include having to deal with unpredictable weather conditions and unforeseen environmental challenges. On the other hand, results drawn from an indoor lab are far more controlled and thus more consistent. When working outdoors, safety also becomes a major risk. If your system goes out of control or falls out of range, it may land on a tree, a home, or even a person. The cage and net structure of the UVS ensures that the system is contained and that the researchers are safe, at all times. Not to mention, the indoor system is much more budget friendly and eliminates the need for transporting equipment and personal to far-off locations. Quanser’s indoor UVS is ready on your campus or research facility and is available for testing when you need it. Once you have tested your control theory on the indoor UVS platform, your team will be better positioned to move your ideas outdoor.
AIAA GNC 2010 delegates had a chance to try flying Quanser's Qball unmanned aerial vehicle.
If you have any further questions, be sure to write us an email at info@quanser.com.
Monday, August 16, 2010
Quanser's 3 DOF Helicopter Helps Researchers at Japan's Kumamoto University
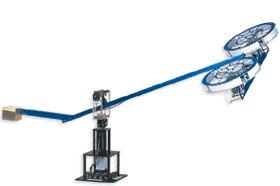
Quanser's 3 DOF Helicopter allows to perform advanced research with applications in areas such as unmanned aerial vehicles.
Back from NI Week
We had the chance to see some amazing fetes in robotics from the RoMeLa robotics lab at Virginia Tech and the Coordinated Robotics Lab at UC San Diego. Our engineers also had a chance to attend some of the sessions at the conference.
Quanser had on display the Active Suspension system and Rotary Family, powered by Labview. We also displayed our QNETs, the experiments that snap on to the NI ELVIS platform.
This year, we had two of our brand new data acquisition cards, the Q2 USB and the QPIDe, running our setup. The first is very portable and can be used with a laptop and the latter is a high powered card for research. The Q2 USB (a Q8 version will be out shortly) is great for taking experiments into the classroom or on the road for demos. It also packs a punch, with the ability to run at up to 2 KHz sampling rates.
The QPIDe is a PCIe hardware-in-the-loop card with an extremely high sampling rate. PCIe has up to 30x the bandwidth of traditional PCI. This card is ideal for research requiring precise measurement or control.
For more info, visit here.
See how the cards look in this video...
Video by Sunny Ray
UVS Demo at AIAA GNC 2010: Announcing the Winner of a HP Netbook
The interactive demo was focused on the Unmanned Vehicle Systems Lab, a new research platform that allows scientists to work with unmanned systems indoors - in a safe and controlled environment. Visitors to the Innovation Hub could not only try to fly the Qball, an unmanned aerial vehicle, they could also enter a draw to win a Hewlett Packard Netbook. The lucky winner is Oleg Yakimenko from the Naval Postgraduate School, Monterey, California. Congratulations!
Sunday, August 15, 2010
Innovative Design Techniques for Mechatronic Devices
Amin Abdossalami, Quanser's R&D Control Design Engineer and Dr. Tom Lee, Maplesoft's Vice President for Application's Engineering will present emerging techniques that are allowing companies to more rapidly design and prototype complex mechatronic devices and products. These include robots, UAV vehicles, haptic devices, automotive systems and many more products and systems that are becoming increasingly important to industry. New development techniques include more thorough and flexible modeling and simulation tools and a greater emphasis on sound, rigorous engineering analytics.
Quanser and Maplesoft are at the forefront of mechatronic design techniques: Quanser, producer of widely adopted mechatronic experiments and research hardware platforms and Maplesoft, producer of advanced physical modeling software tools for control and mechatronic applications.
The webinar will provide an overview of advanced modeling techniques and real application case studies, including UAV applications and haptic devices. From a software perspective, MapleSim system will be highlighted as an example of modern system modeling tools that are beginning to change the way engineers approach complex design. Overall, the audience will gain clear insight into the modern toolchain and workflow, the core benefits of the covered techniques, and the essential techniques for rapid mechatronic system development.
Click here to register for the webinar.